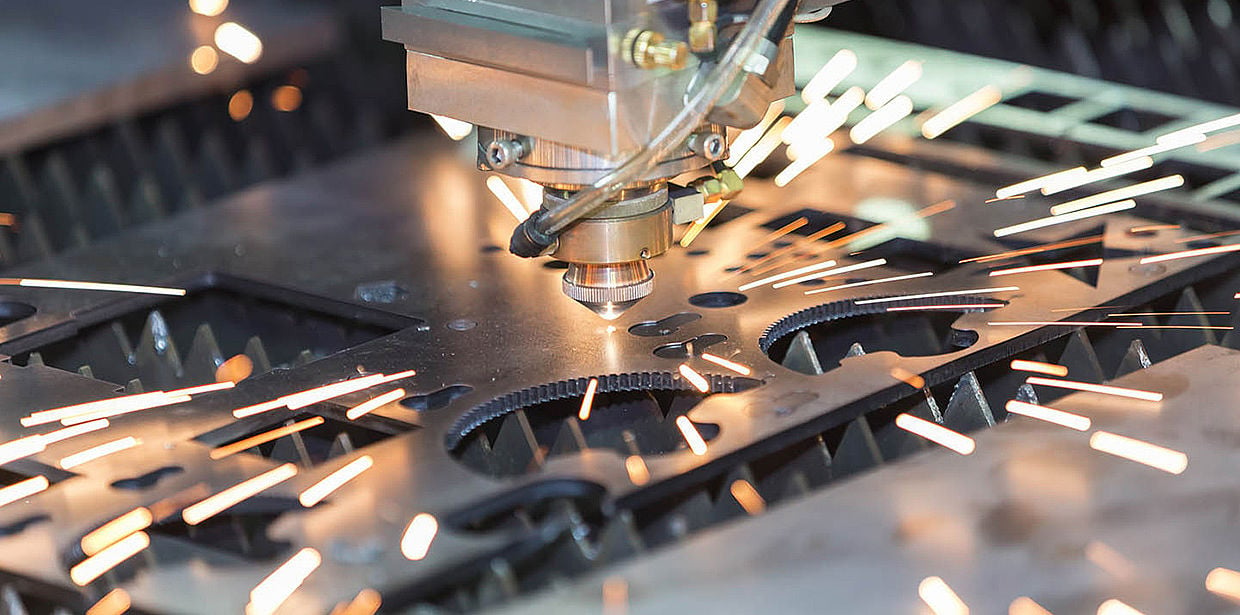
Satisfied customers due to perfect parts – 3 tips for laser job shops.
Generally, a laser job shop offers a wide range of services to meet all of the possible customer requirements. In addition to punching, laser cutting, welding and forming as well as laser marking or forming, this also includes leveling and deburring sheet metal. When a laser or punching tool is used for sheet metal processing, the parts generally need to be corrected afterward.
Processing with a laser causes a vast amount of heat precisely where the beam hits the material. After cutting, hidden stresses are often released within the sheet metal. At the same time, hardening occurs at the edges and – due to the enormous temperatures – stresses form within the metal sheet. This results in flatness defects, which cause the sheets to warp. In turn, this impairs the effectiveness of downstream processing. Furthermore, the laser cutting process can result in the formation of burrs. These are also less than optimal for problem-free and rapid downstream processing. Leveling and deburring the parts are the only solutions in this case. For any laser job shop, flexibility combined with ease of operation are essential as sheet metal parts with varying thicknesses and widths are processed every day. With the right roller leveler or deburring machine, this is no problem at all.
7 success factors for efficient processes.
From automated warehouses to intelligently linked machines: find out which factors help to ensure efficient sheet metal processing.
Download: Success factors for efficient sheet metal processing
Yet leveling and deburring does not have to be a challenge.
At the same time, metal parts with different thicknesses and part widths are not the only challenge a laser job shop has to deal with. Changing material types and parts with various cutouts are further aspects. Meeting all of the customer requirements demands flexible, fast and – most importantly – high-quality processing. This is not generally a problem for modern leveling and deburring machines. Nevertheless, a laser job shop needs to consider a few things when choosing a machine in order to be on the safe side in terms of high-quality and time-efficient leveling and deburring. These are the three crucial tips:
1. Quickly select the right setting, thanks to ease of operation.
Processing a wide variety of different parts is very common for laser job shops. To avoid delays, it is important that the roller leveler or deburring machine can quickly be adjusted and configured for each specific component. An intuitive human-machine interface makes it easy for the – often changing – machine operators to quickly find the desired setting.
A machine with hydraulic feed, for example, offers a considerable advantage when it comes to leveling. The high-performance hydraulic cylinders ensure rapid and precise configuration and control of the leveler. Supported by an intelligent control system, the machine automatically calculates the settings without time-consuming programming. With their unique performance capabilities, hydraulic levelers guarantee the best leveling results, especially with laser parts and also punched and flame, oxyfuel and plasma cut parts.
Today, modern machine control systems also help operators to quickly find the right deburring or rounding results. Such functions can include automatic measurement and compensation of the consumables, integrated operating guides or maintenance schedules. We also offer a barcode scanner that provides the user with the correct machine settings for the job at the touch of a button, for example.
If the user interfaces for the leveling and deburring machines also have largely identical displays, the operator can familiarize himself with the machines twice as quickly and easily.
2. A wide processing spectrum for uncompromising quality.
Another essential aspect for the work at a laser job shop: problem-free processing of parts with various shapes and cutouts. Especially parts with large cutouts require precise processing. The distance between the upper and lower leveling rollers is the key factor for the roller leveler. This leveling gap has a direct impact on the results. During the leveling process, both the material and the machine itself are subjected to massive forces. These forces also change continuously, especially when leveling a part with different cross sections. Therefore, it is important that the leveling gap remains constant despite the changing leveling forces. A servo-hydraulic leveling gap control system handles this with unmatched speed and, therefore, plays a key role in achieving optimum leveling results.
In this regard, laser job shops will benefit from relying on the newer generation of roller levelers. These are generally equipped with a servo-hydraulic leveling gap control. If the leveling gap changes as components pass through the machine, an integrated sensor detects the changing characteristics. The servo-hydraulics then ensure that the leveling gap is readjusted within fractions of a second, remaining at the set value. This is the optimum solution for components with cutouts and varying shapes.
3. One pass – one result.
Time and efficiency are often crucial given the highly competitive industry. The design of the production processes provides time-saving potential. The ability to fabricate finished sheet metal parts as quickly and with as few steps as possible should be a top priority when selecting the right leveling or deburring machine.
Some deburring machines process metal sheets on both sides in one pass. In contrast to machines that work from just one side at a time, the sheet metal only has to be fed through the machine once. This cuts both the processing time and personnel costs on the deburring machine in half. The following example shows just how quickly this pays off: If half a shift per working day can be saved on a deburring machine operated by two workers, this generates annual personnel cost savings of approximately 75,000 euros.
Linking machines also offers a lot of potential for savings. If, for example, you link your deburring machine with the leveler via roller conveyors, double-sided processing in one pass becomes indispensable.
One machine for every need – one final tip.
Sheet metal is not just sheet metal. Every sheet metal processing industry produces parts for different applications. In turn, these all have different machining requirements. For the levelers or deburring machines used at the laser job shops, this means maximum flexibility is crucial. Because flexible work at high speed while delivering excellent quality is a big advantage for a laser job shop. In order to find a consistent solution for your production, you should focus on the key products that you process rather than trying to consider all of the custom project when selecting your machine. This approach keeps your investments within reasonable bounds. At the same time, this also enables you to install controllable and efficient sheet metal working processes.
7 success factors for efficient processes.
From automated warehouses to intelligently linked machines: find out which factors help to ensure efficient sheet metal processing.
Download: Success factors for efficient sheet metal processing
More contributions
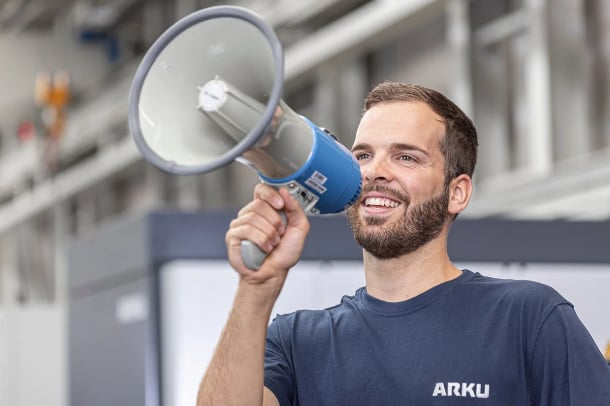
ARKU Newsletter
Exciting events, informative case studies, practical expert tips: With the ARKU Newsletter you are always well informed.
Additional information.
Contact.
ARKU Maschinenbau GmbH
Siemensstraße 11
76532 Baden-Baden / Germany
T: +49 7221 5009-0
F: +49 7221 5009-11
Keep up with the leaders: with our newsletter.
Machines in use at customers, practical tips, events and much more: keep up with the news in the ARKU world.