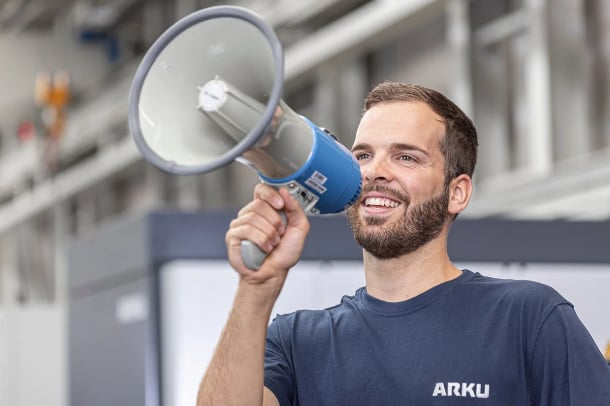
ARKU Newsletter
Exciting events, informative case studies, practical expert tips: With the ARKU Newsletter you are always well informed.
Whether from the coil or from the blank - in order for the final quality to be right, the sheets must be leveled and deburred. There is a whole range of machining processes that run more reliably and precisely with perfect sheets. In this article, we will reveal what these are.
When working from coil, the rule is: as little downtime as possible on the coil! For maximum productivity of punching machines and presses, coil lines are available in short or long design. A leveling unit is always included, which at least eliminates coil curvature. With a high-quality leveling unit, constant drawing ratios can also be achieved. This makes forming easier, tool consumption and variance are lower - and users save storage costs.
In fineblanking, good coil guidance ensures high stroke rates. With their leveling unit, the coil lines enable fast and efficient production. With precise feed technology, even tight component tolerances can be maintained. And they do so permanently and consistently reproducibly. This means that even complex components are no problem.
In the profiling process, the coil preparation lines enter into a symbiotic relationship with the profiling lines. Pre-punching, strip end welding and strip accumulator systems can be components of a coil preparation line. Together with the leveling unit, they ensure perfect results and high productivity.
The coils often have to be cut into manageable pieces. When cutting to size, a high-performance leveler in ARKU's slitting and cut-to-length lines ensures flat, low-stress blanks and uniform surfaces. With the rotating shears, users achieve tight tolerances in the end product. And subsequent processes can run consistently in this way.
When working from the sheet, laser cutting is now one of the most important processes. Levelers ensure flat and stress-free parts after laser cutting. This creates optimum conditions for subsequent processes such as bending, welding, painting or electroplating.
Flame cutting or plasma cutting is usually best suited for cutting thick sheets. However, these cutting processes easily produce slag and burrs. The high energy input during cutting can also lead to stresses and unevenness in the sheet metal parts. This makes subsequent work more difficult. Part levelers and deburring machines provide a remedy and ensure greater process reliability and cost-effectiveness. Even flame-cut parts become uniform through deburring. At the same time, working conditions for employees are improved: deburred parts allow easier handling and reduce the risk of injury.
For bending, angles and components must be precisely machined - especially in automated production. Part levelers ensure optimum preparatory work, the parts are stress-relieved and level. Deburring machines ensure burr-free and rounded sheets that are optimally prepared for subsequent work. This enables employees to work more efficiently and safely.
During punching, machine leveling, deburring and rounding ensure uniform punched parts. The leveling process makes the sheets stress-relieved and flat. The unavoidable punching burr is removed by a deburring machine. Maintained tolerances and an improved feel prepare the parts for subsequent processes such as bending, folding and welding. Painting or electroplating is also simplified. Automated processes with consistent quality make the plants more productive and safer.
If the sheet metal parts are leveled and deburred before welding, this saves valuable time. The parts can be mounted more easily and quickly in the welding fixtures, welding is faster and finished welding assemblies no longer need to be reworked. Robot welding in particular becomes safer thanks to part levelers and deburring machines, as the welding gap is correct.
Conclusion: The leveling and deburring of sheet metal is not a luxury, but contributes significantly to productivity in sheet metal processing. Therefore, these processes should not be missing in any sheet metal processing.
Exciting events, informative case studies, practical expert tips: With the ARKU Newsletter you are always well informed.
ARKU Inc.
7251 E. Kemper Road
45249 Cincinnati, OH / USA
P: +1 513 985 0500
F: +1 513 985 0580
Machines in use at customers, practical tips, events and much more: Find out what's new in the ARKU world.
ARKU Inc. © 2023 Mail info-us@arku.com Tel. +1 513 985 0500