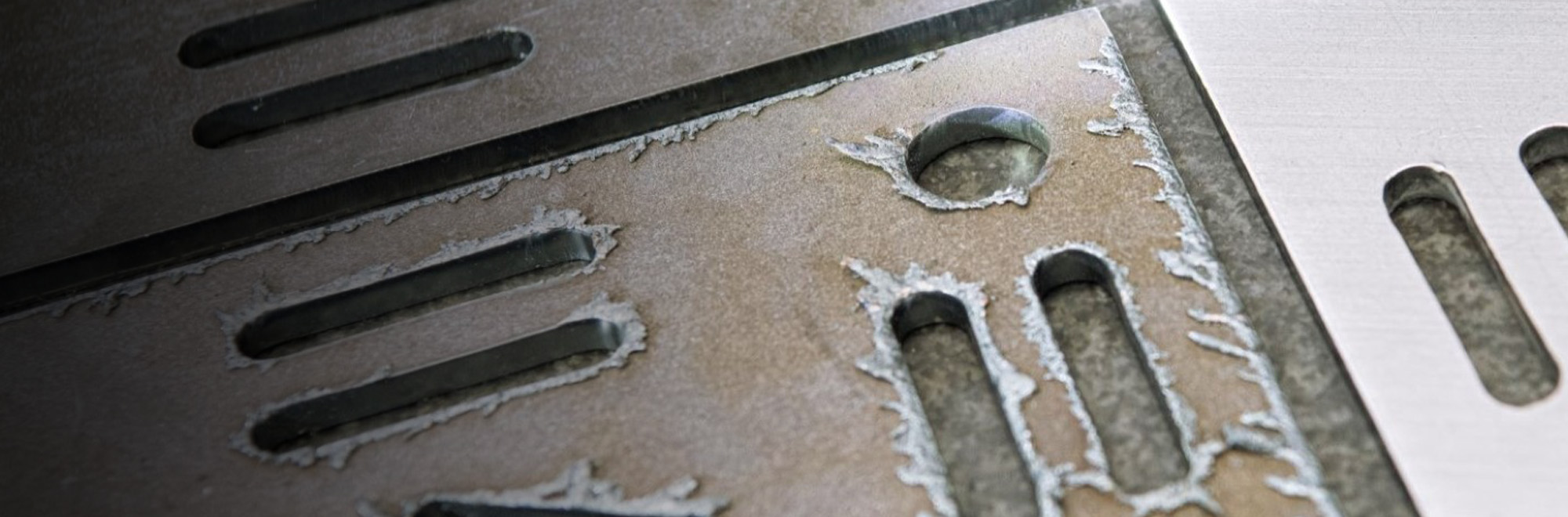
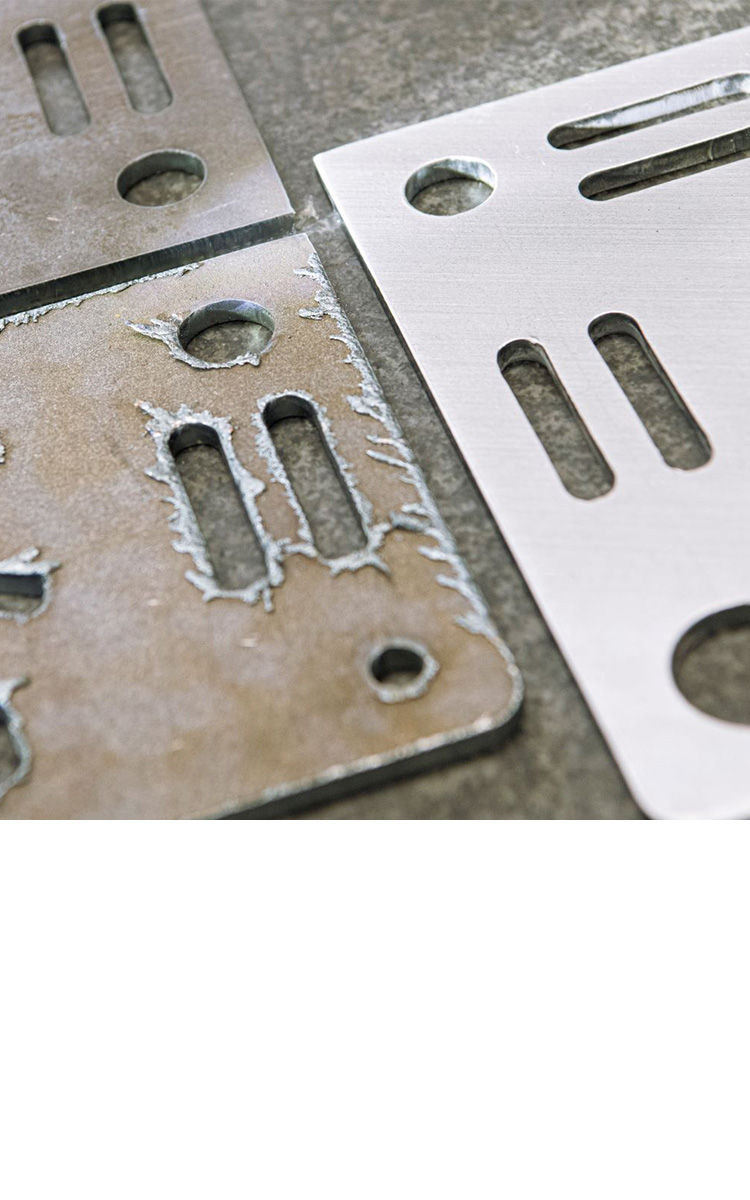
The completely automated line for double-sided deslagging, deburring and edge rounding of plasma cut and flame cut parts and heavy plates.
EdgeBreaker® 9000 Line
Heavy Plate & Parts Slag Removal Line
More throughput. Less effort. Reproducible quality. Sounds too good to be true? Thanks to the double-sided processing of the EdgeBreaker® 9000 LINE, this is possible. The EdgeBreaker® 9000 LINE takes over the complete processing of your flame cut parts after plasma and oxyfuel cutting in just a single pass
- Remove slag
- Deburr
- Round edges
Your Advantages as an Overview
Double-sided deburring and edge rounding
The EdgeBreaker® 4000 processes flame, plasma and oxyfuel cut metal parts or plates on both sides in just a single pass. You will save up to 50% of time compared to working with single-sided machines.
Tool storage for saving processing parameters
If you produce the same metal plate or part from time to time, you can save the processing settings directly in the machine and call upon the values when required. This allows you to quickly setup the deburring machine for repeat production runs. Thus, avoiding errors during setup.
Automatic wear compensation for abrasives
For consistent results, it is essential to always know where you stand. The EdgeBreaker® 4000 measures the remaining length of your edge rounding tools (abrasives) within the machine and automatically compensates for the wear off. Leaving you with consistent results from beginning till end of the tools life.
Simple operation and maintenance for the deburring machine
The graphical touchscreen HMI is very intuitive and easy to operate. It supports you in setting up the machine and provides tips on operation and maintenance. It can even be used while wearing gloves. For efficient processing without errors.
Future-proof solution with the ARKU Connect
Various other processes, such as blasting systems, parts levelers and robotics, can be easily linked to the system via ARKU Connect. This Industry 4.0 preparation makes the EdgeBreaker® 9000 LINE particularly future-proof and expandable.
Option for separate machine usage
The EdgeBreaker® 9000 LINE features the two deburring machines EdgeBreaker® 5000 MAX and EdgeBreaker® 4000. Both machines can also be used independently, providing maximum flexibility for future needs.
The Best of Both Worlds
With the EdgeBreaker® 9000 LINE you will receive our top machines for flame cut parts: The unique pin system from the EdgeBreaker® 5000 MAX ensures you reliable slag removal even with poor cutting qualities. The proven quick-change system of the deburring and rounding tools from the EdgeBreaker® 4000 eliminates downtimes via fast and tool-free exchange of brushes and the sand paper.
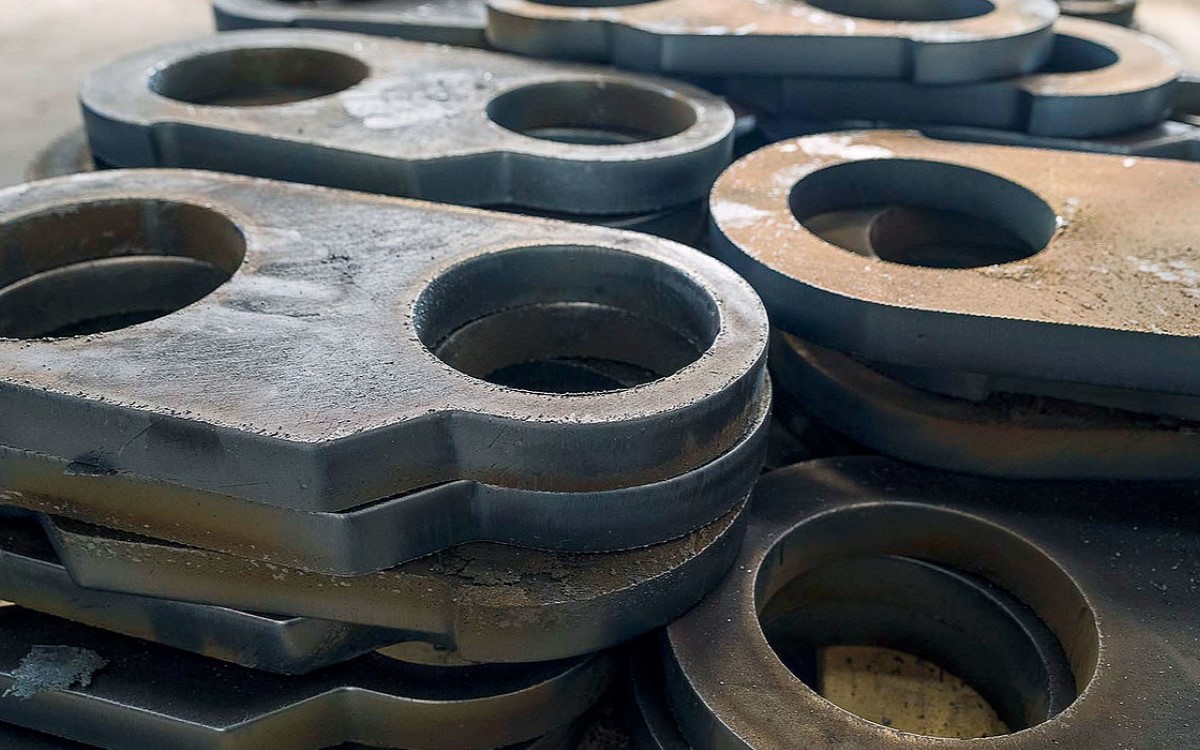
Increase Throughput in the Blink of an Eye - instead of Time-consuming Parts Flipping
Thanks to edge rounding and slag removal on both sides, your flame cut parts are completely processed in just a single pass. A time-consuming and nerve-racking second pass with complex parts handling is a thing of the past. You save valuable time in during processing and improve the working conditions of your employees.
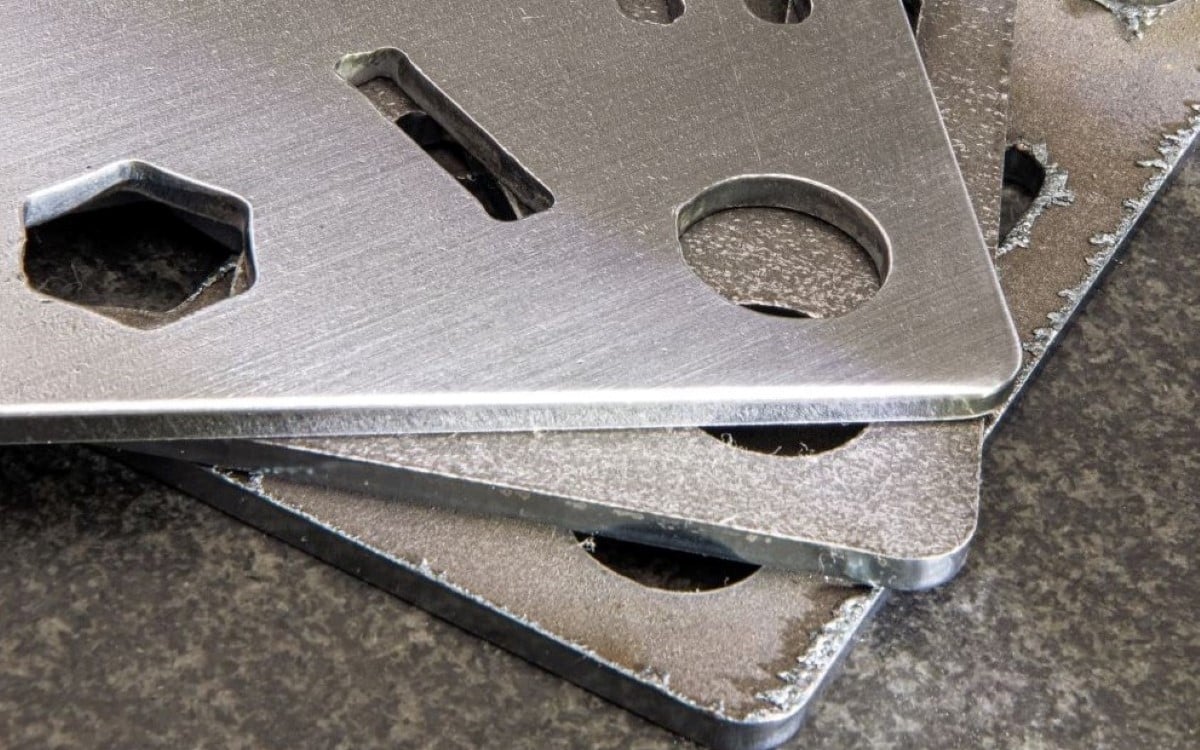
Productivity Booster thanks to Consistency and Reliability
With the EdgeBreaker® 9000 LINE, you can rely on your machines to achieve the consistent high-end processing results on your material edges. Spending time second guessing the optimal settings is a thing of the past. Rejects and complaints are also reduced. You save valuable time and money while achieving consistently high-quality for your flame-cut parts.
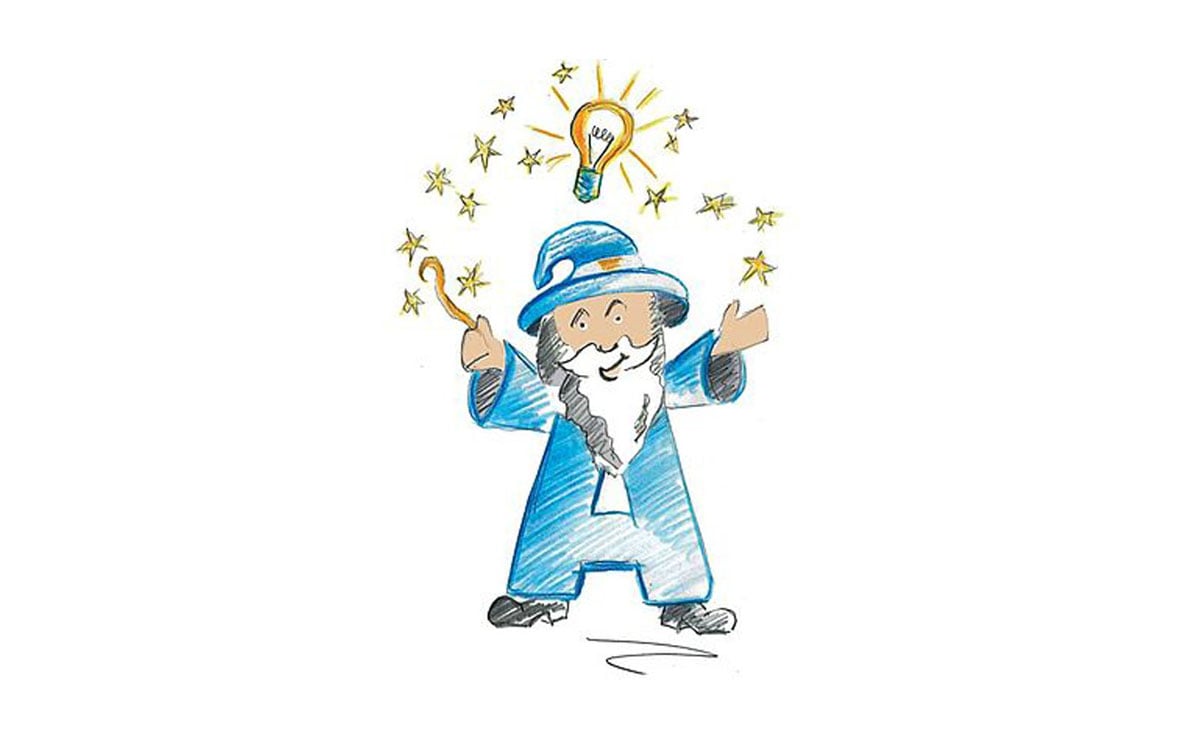
Always the Ideal Processing Settings – with the ARKU Wizard
The ARKU Wizard is an intelligent software that helps its operators to automatically adjust the processing settings of their deburring machine. During the process, the material, tool and machine data are linked together. Only four parameters (material, size of burrs, material thickness, desired edge rounding) need to be entered. The tools available to the operator are stored in the Wizard. The software automatically selects the best deburring tool for the particular processing requirement(s). In doing so, the Wizard always optimally adjusts the deburring machine to achieve maximum productivity and minimal tool wear. In this way, operators can be sure of achieving the desired processing results with minimum effort and no time wasted.
Processing Features for every Requirement
ARKU has developed various modules for processing sheet metal parts to ensure the highest quality, reliable processes and individual, customized solutions that meet your requirements.
Frequently Asked Questions
Suitable Tools
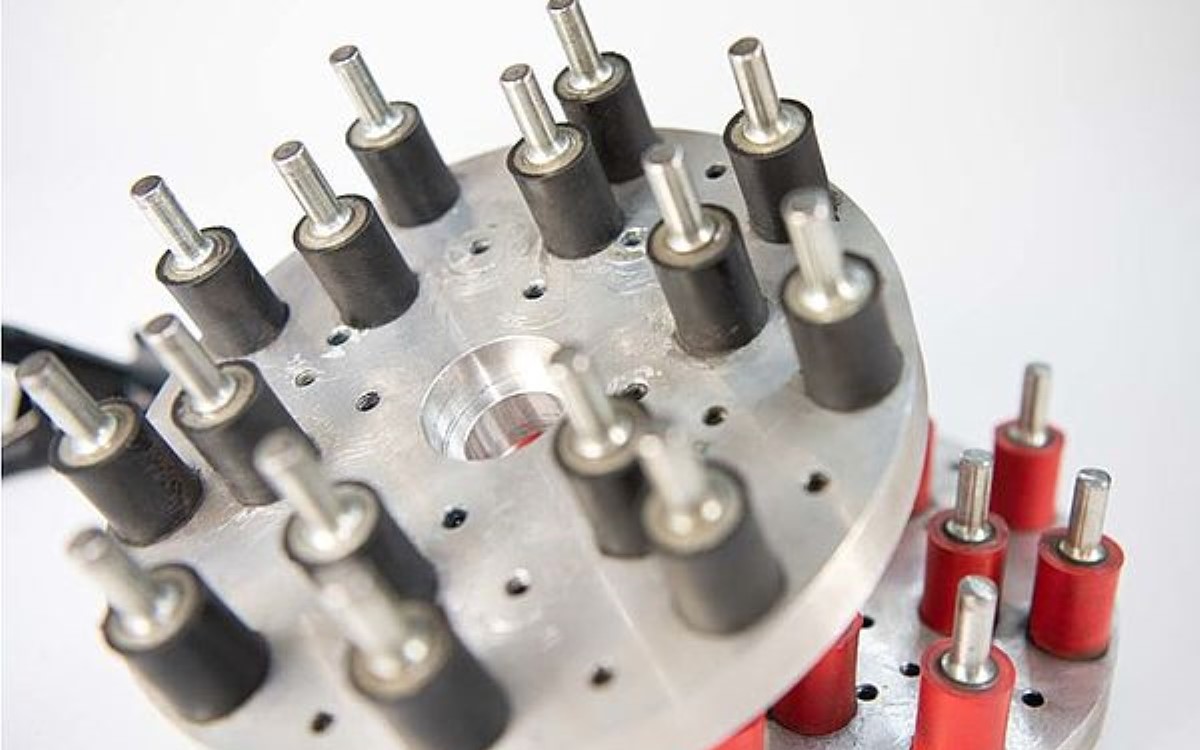
Discs to remove slag
Slag hammer to remove slag.
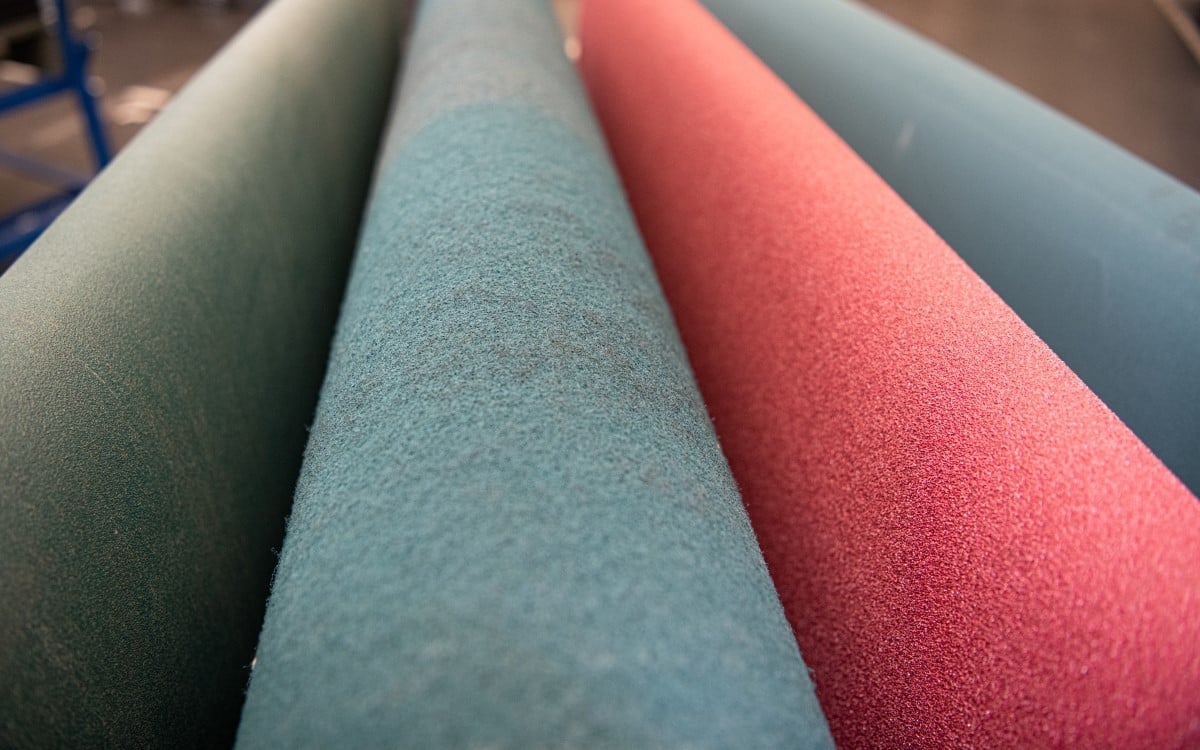
Abrasive belts
Abrasive belts to deburr sheet metal parts.
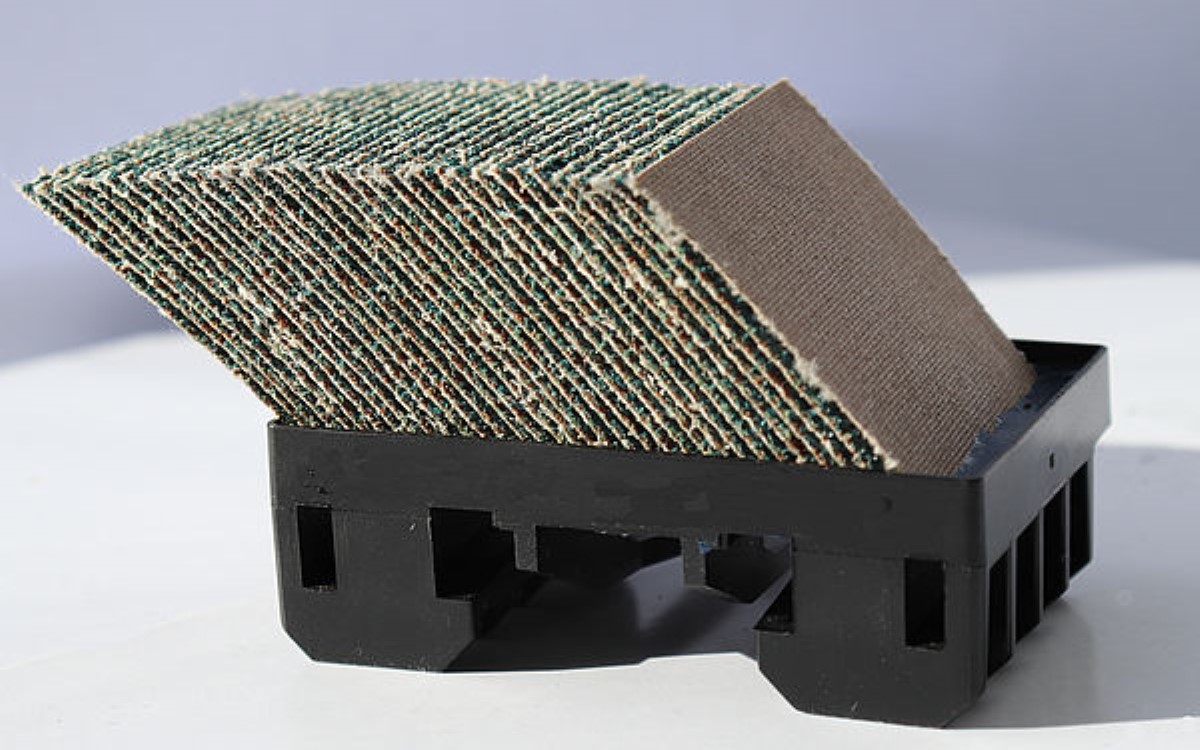
Blocks for deburring
To remove burrs on laser-cut or punched parts.
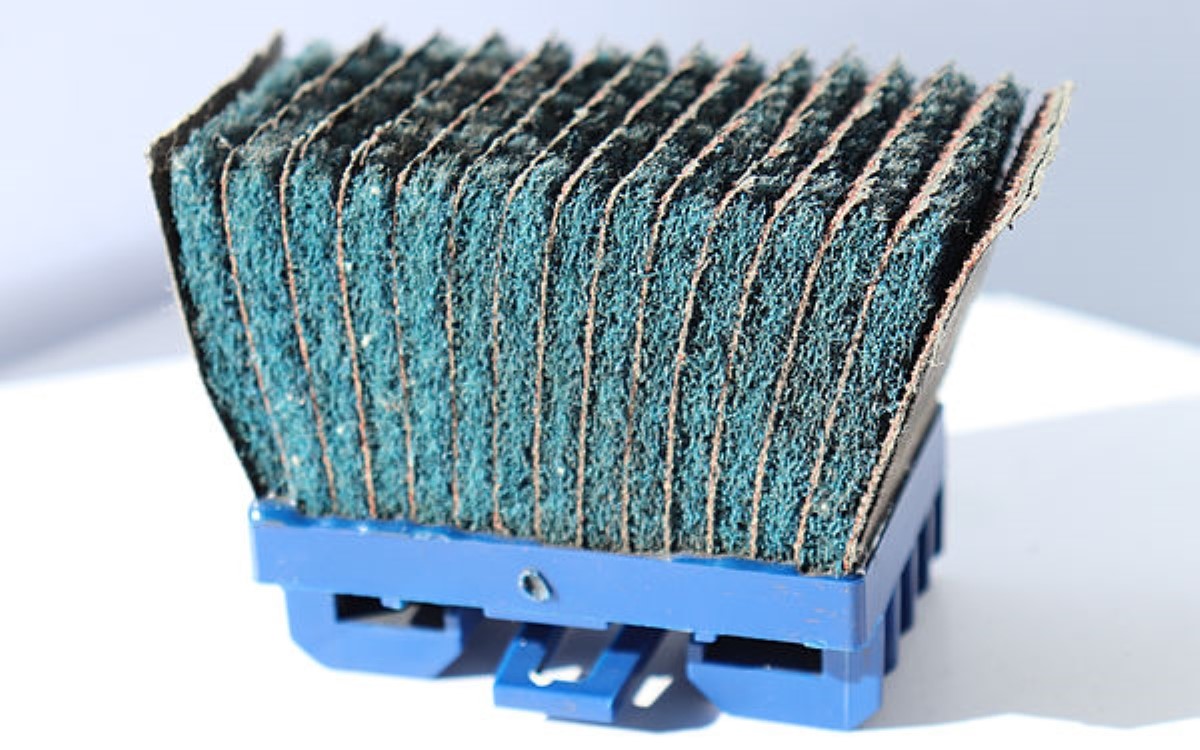
Blocks for edge rounding
To round the edges including the inner and outer contours.
Related machines
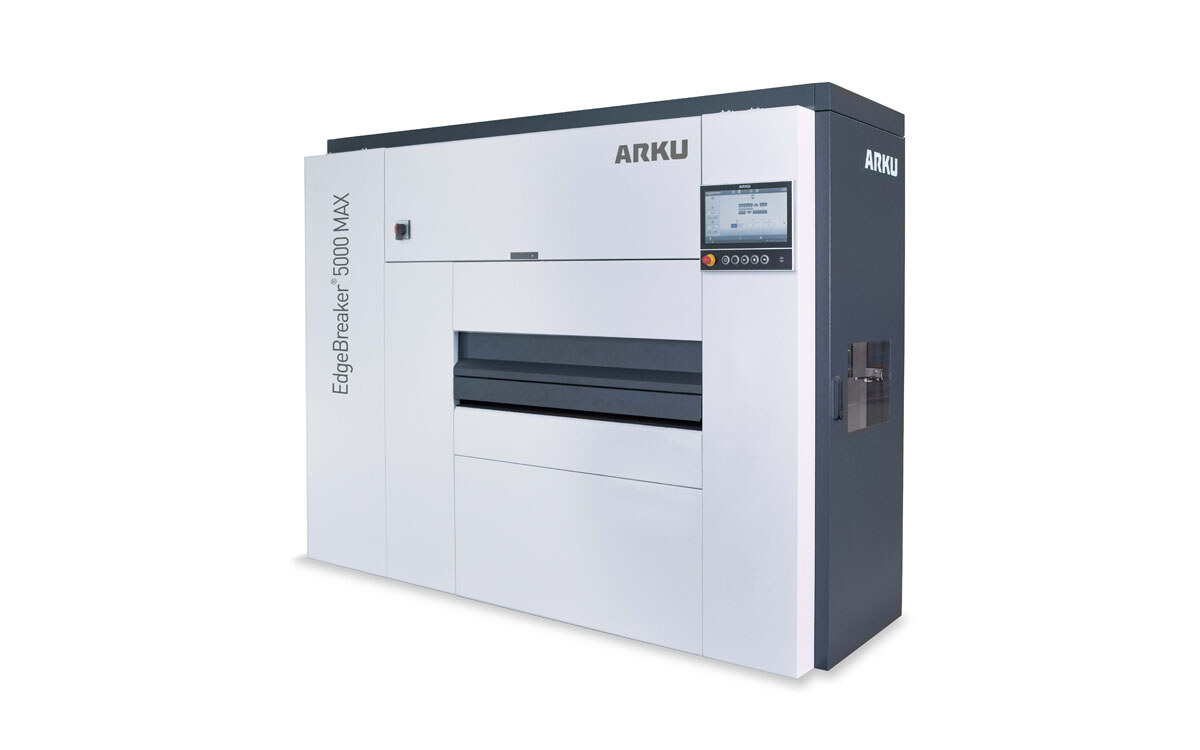
EdgeBreaker® 5000 MAX
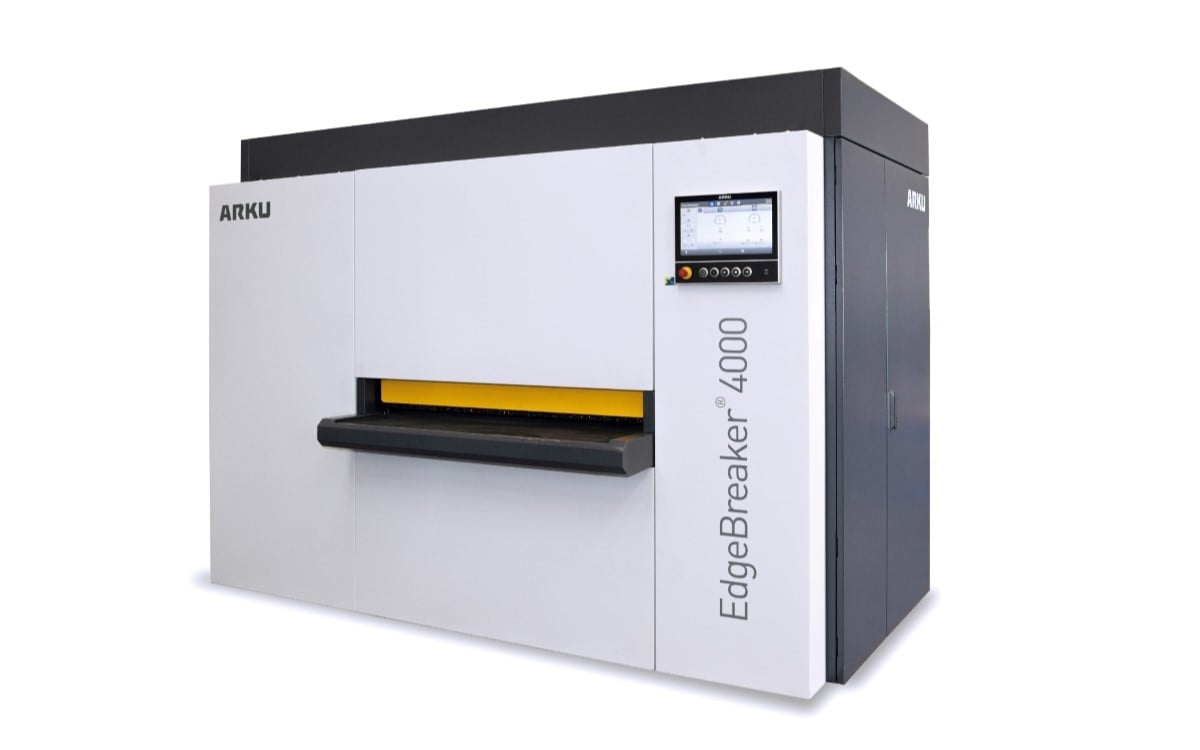
EdgeBreaker® 4000
The ultimate powerhouse for flame cut parts featuring a heavy-duty grinding drum.
Material thickness: 0.03" - 4" (0.8 - 100 mm).