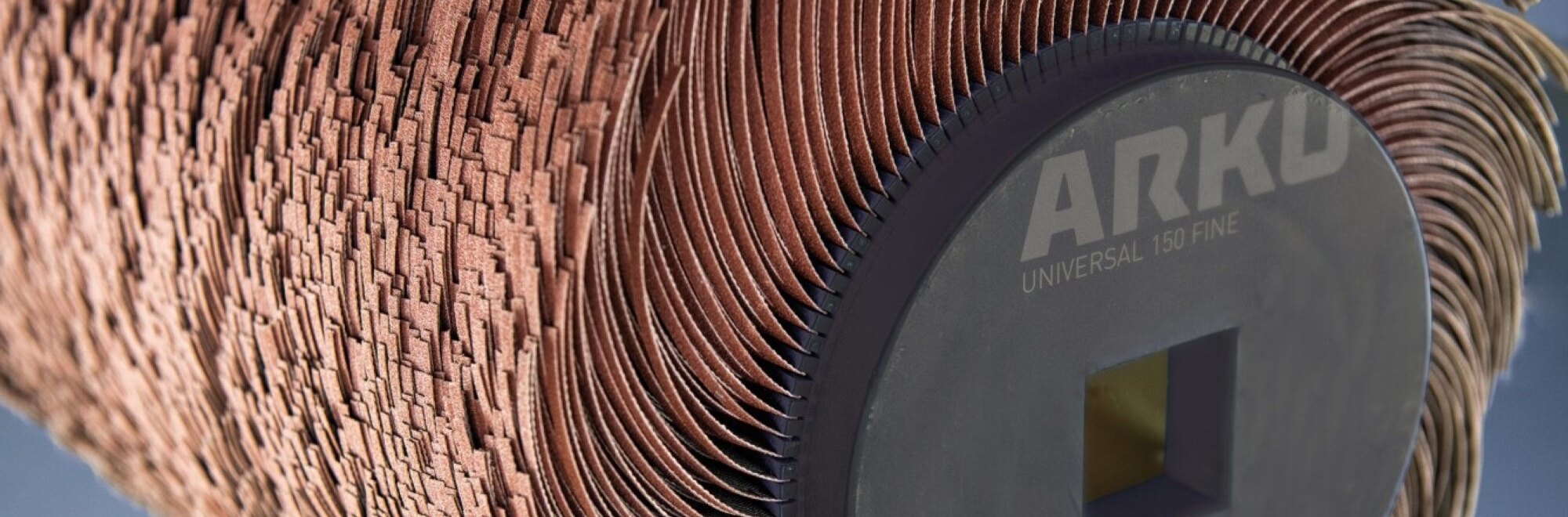

Our ARKU machines are effectively used in sheet metal processing worldwide. We offer a tested selection of premium spare parts and deburring machine tools - delivering optimal processing results.
Deburring Tools for an Optimal Results
Our high quality standards do not only apply to our deburring machines, but to our deburring tools as well. We place great emphasis on the material quality, precision manufacturing and enhanced lifetimes of spare and wear parts. Most often, successful processing depends on the small things. So we offer you only tools that will be able to complete the job correctly, the first time. In our ARKU online store, you can find suitable tools and wear parts for your deburring machine.
General Advantages of Deburring Tools from ARKU
Material quality
Precision manufacturing
Economic efficiency
ARKU Online Shop
Deburring Blocks
ARKU deburring blocks have been specifically designed for this purpose: To deburr and edge round sheet metal as efficiently as possible. The patented tools enable double-sided processing of your parts in a single pass. The tools are changed within seconds via a simple click. Depending on the requirements of your sheet metal, the machine can be equipped with tools for deburring or edge rounding.
ARKU deburring blocks at a glance
- Processing of your metal sheet on both sides becomes possible
- Click system for a fast tool change
- Uniform wear (regardless of the inserted position)
- Long tool life
- Various designs available
Technical data
Width | approx. 50 mm (2”) |
Length | approx. 75 mm (3”) |
Height | approx. 50 mm (2”) |
Shape | Preferential direction available |
Machine models | EdgeBreaker® 2000, 3000, 4000 |
Processes | Deburring, edge rounding, oxide removal |
Variants
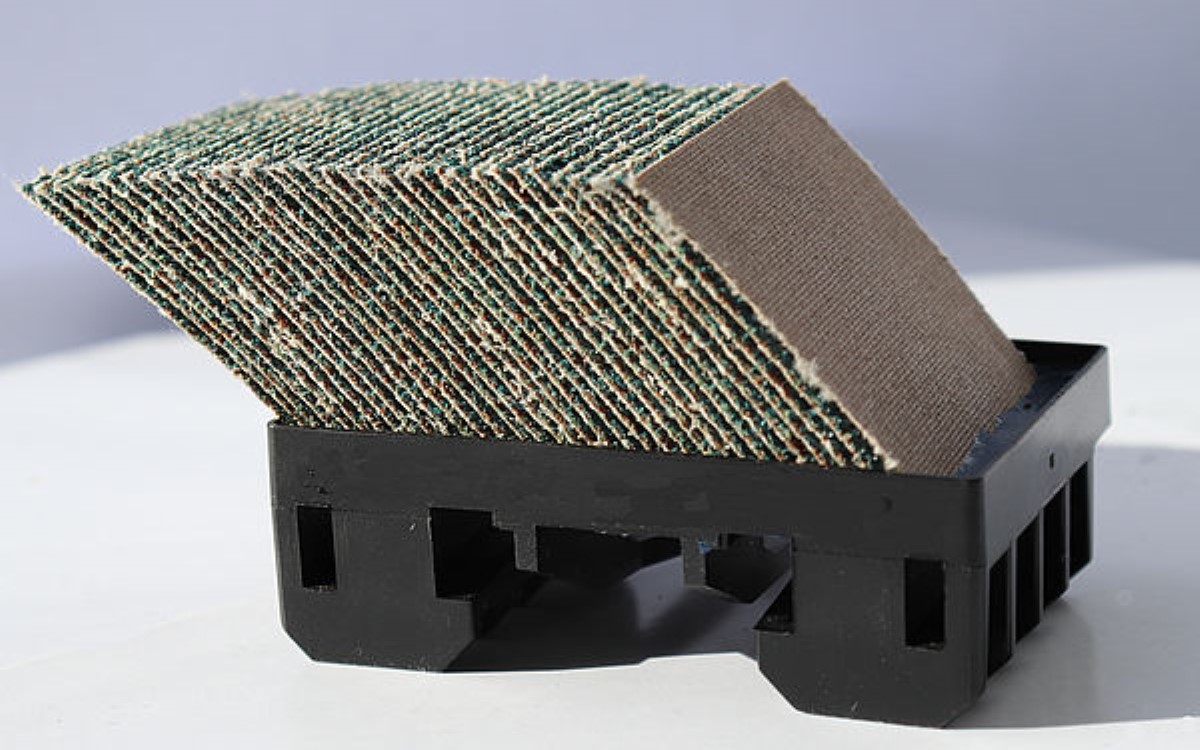
Blocks for deburring
To remove burrs on laser-cut or punched parts.
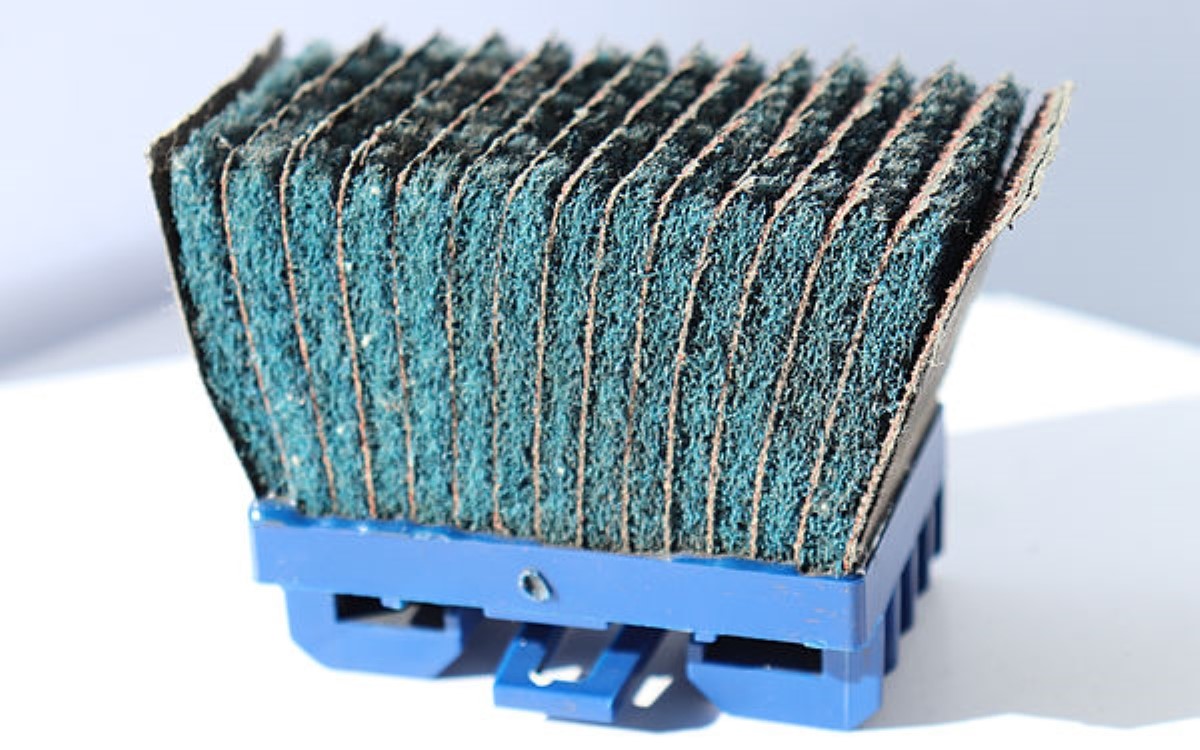
Blocks for edge rounding
To round the edges including the inner and outer contours.
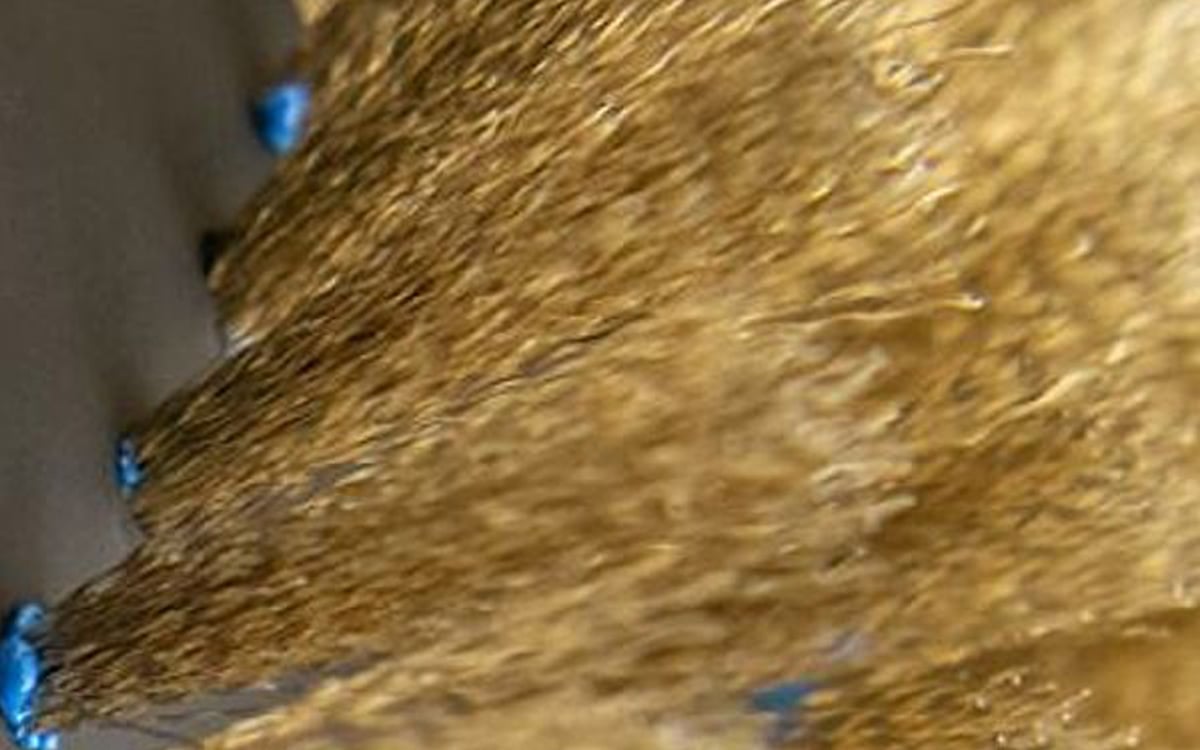
Blocks to remove oxide
To remove oxide from the cutting edges.
FAQs
Rotary & Roller Brushes
ARKU rotary & roller brushes ensure the best possible and uniform rounding of sheet metal edges. The brushes rotate across several axes and can thus strike all the sheet metal edges multiple times. A radius of up to 2.0 mm is possible for some applications. The tools come in various designs so you can influence the degree of rounding on your parts, as well as the surface or the processing speed. Depending on your processing requirements, we will select the suitable roller brush together with you.
ARKU rotary & roller brushes at a glance
- Best possible sheet metal edge rounding
- Uniform rounding
- Very fast tool change
- Direction-independent processing
- Long tool life (up to 3000 hours)
- Various designs available
Technical data
Diameter | approx. 350 mm (14”) |
Width | approx. 500 mm (20”) |
Shape | Uniform rounding of all sheet metal edges |
Machine models | EdgeBreaker® 6000 |
Processes | Edge rounding, Oxide removal |
Variants
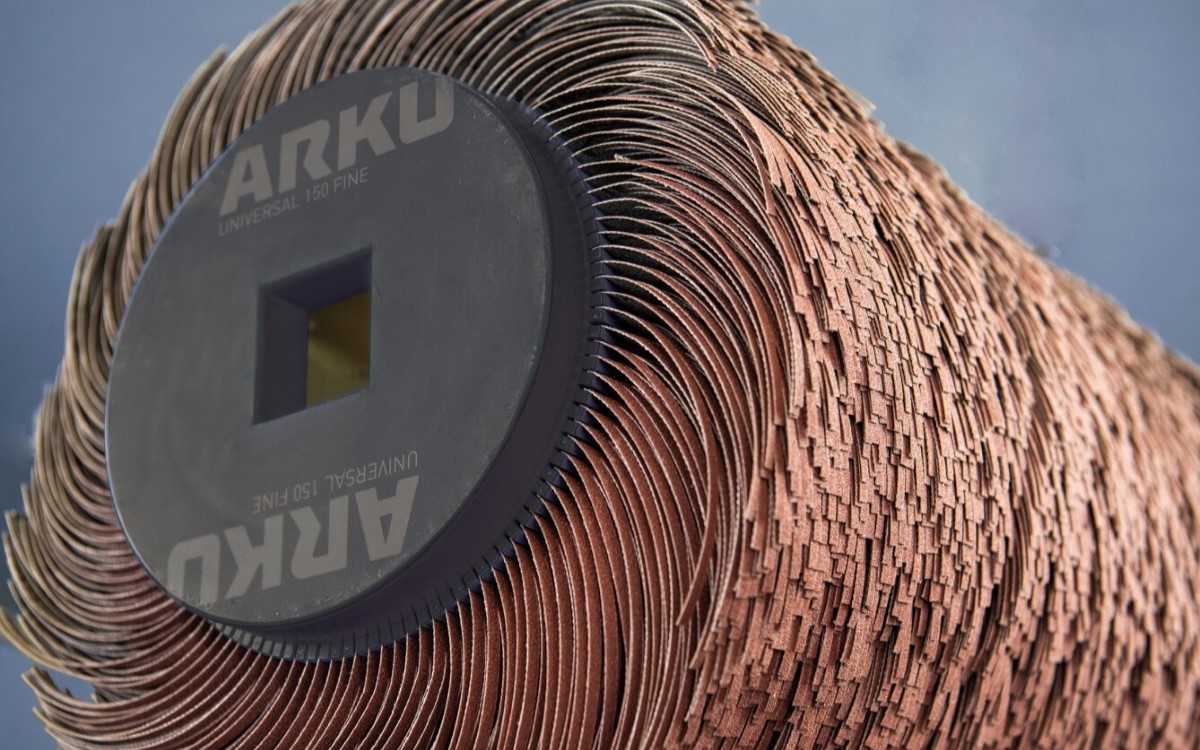
Rotary brushes for rounding
From the universal original to the custom-made tool for your specific application.
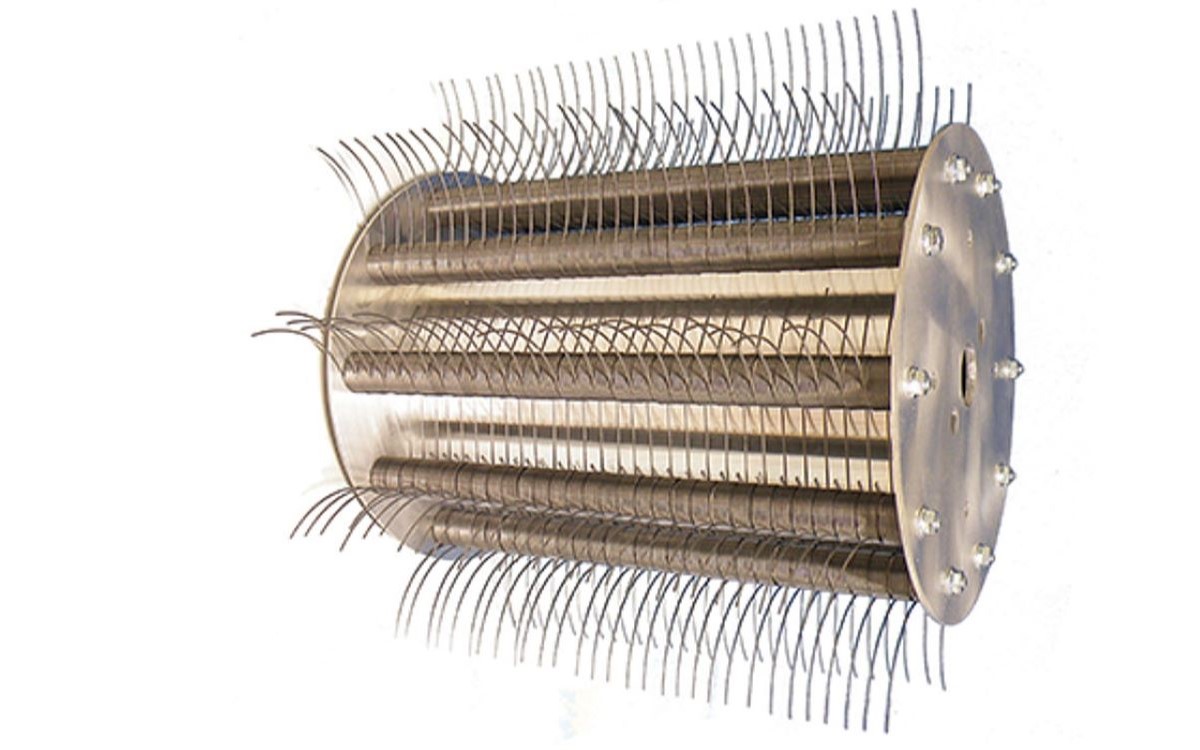
Roller brushes for oxide removal
A special purpose tool for the removal of oxide byproducts from your cutting edges.
FAQs
Disc Brushes
ARKU disc brushes ensure good processing results. Depending on the application, different designs are used. While our slag hammer simply chips off the slag, discs with abrasive filaments ensure the non-directional edge rounding of your sheet metal edges. Even oxide removal can be accomplished with ARKU disc brushes by using the appropriate machine.
ARKU disc brushes at a glance
- Non-directional processing
- Sustainable: Brush elements can be separately inserted into a base
- Uniform wear (regardless of the inserted position)
- Various designs available
Technical data
Diameter | approx. 200 - 350 mm (8” – 14”) |
Height | approx. 50 mm (2”) |
Shape | Uniform contours |
Machine models | EdgeBreaker® 1000, 5000, EdgeRacer |
Processes | Slag removal, edge rounding, oxide removal |
Variants
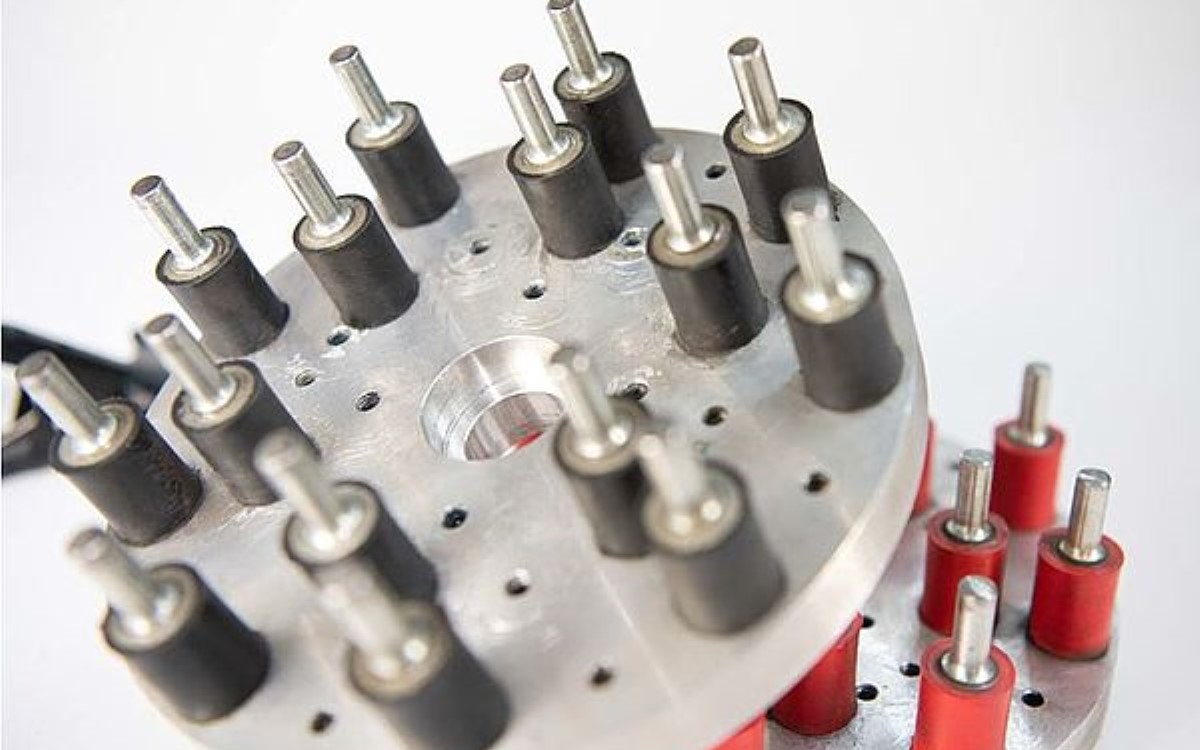
Discs to remove slag
Slag hammer to remove slag.
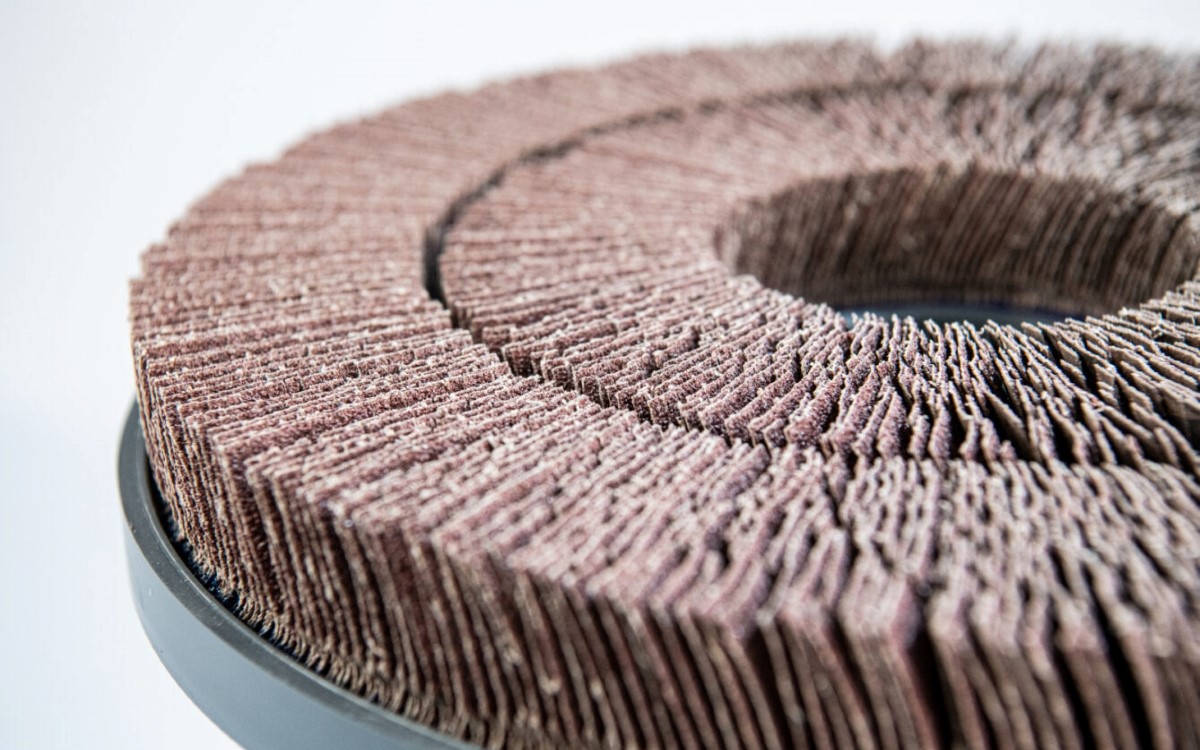
Discs to deburr and edge round
Non-directional deburring and edge rounding of sheet metal edges.
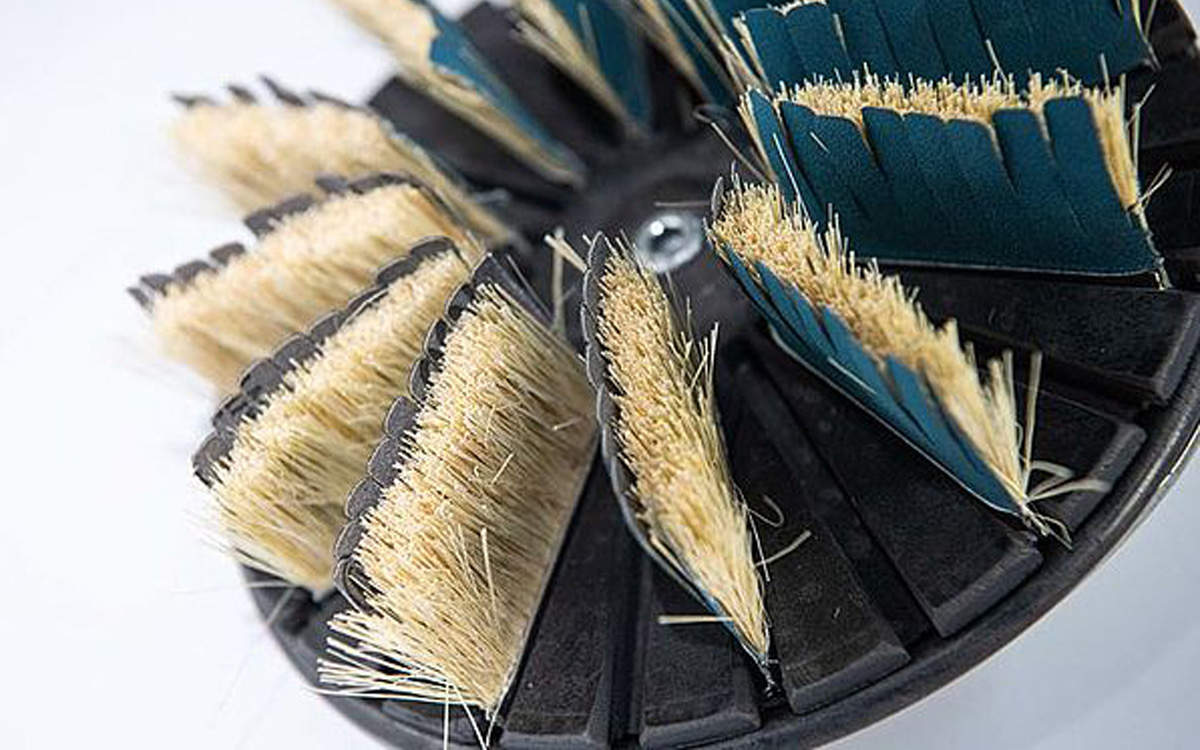
Discs to remove oxide
Specifically designed for the removal of oxide along the cutting edges.
FAQs
Abrasive Belts & Non-woven Abrasives
Abrasive belts remove the burr from the part’s edge. This is usually the first step performed by the deburring machine. At the very end is surface finishing of the sheet metal, if desired. The associated non-woven abrasives deliver the necessary texture to the sheet metal. ARKU abrasive belts and non-woven abrasives are available in different designs. Ask us about the options that improve your deburring process by the choice of the ideal abrasive belts and non-woven abrasives.
ARKU abrasive belts and non-woven abrasives at a glance
- Verified quality from the manufacturer
- Optimal choice of abrasives
- Short delivery times
- Optimal interplay of tool and machine
- Expert advice
Technical data
Dimensions |
approx. 260 mm x 2087 mm (10” x 82”) |
Shape | Uniform edge rounding of all sheet metal edges |
Machine models | EdgeBreaker® 1000, 4000, 6000 |
Processes | Deburring, surface finishing |
Variants
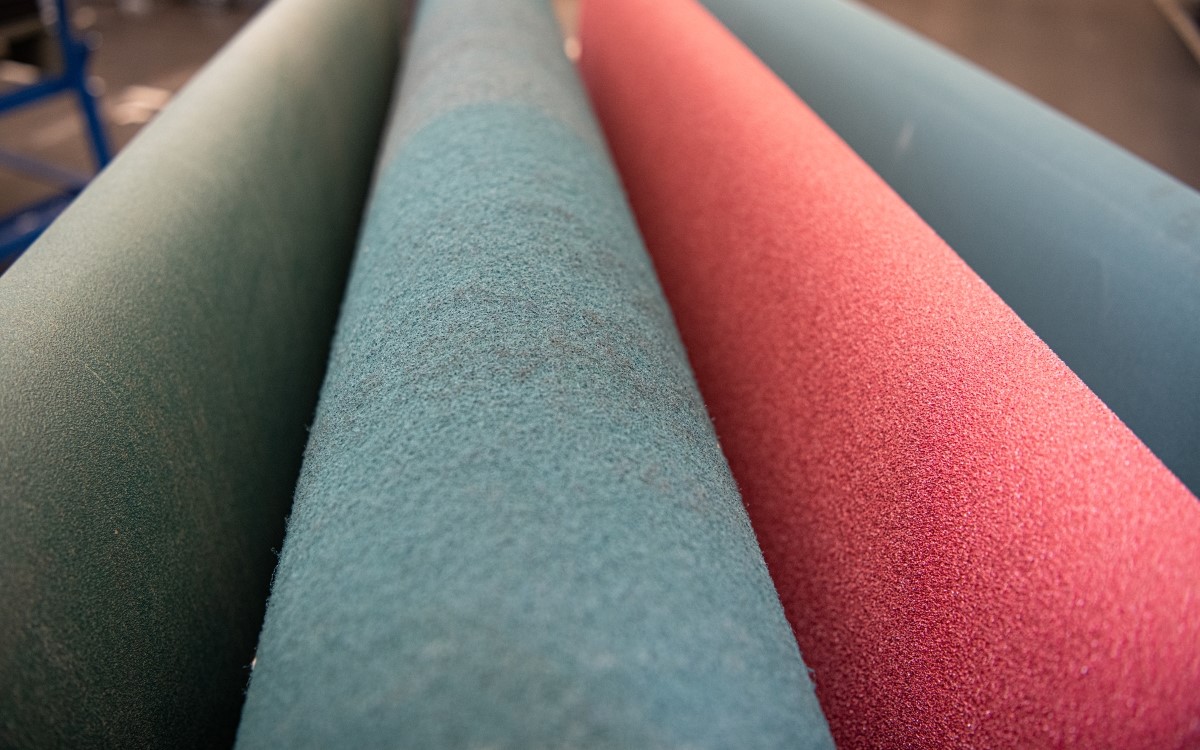
Abrasive belts
Abrasive belts to deburr sheet metal parts.
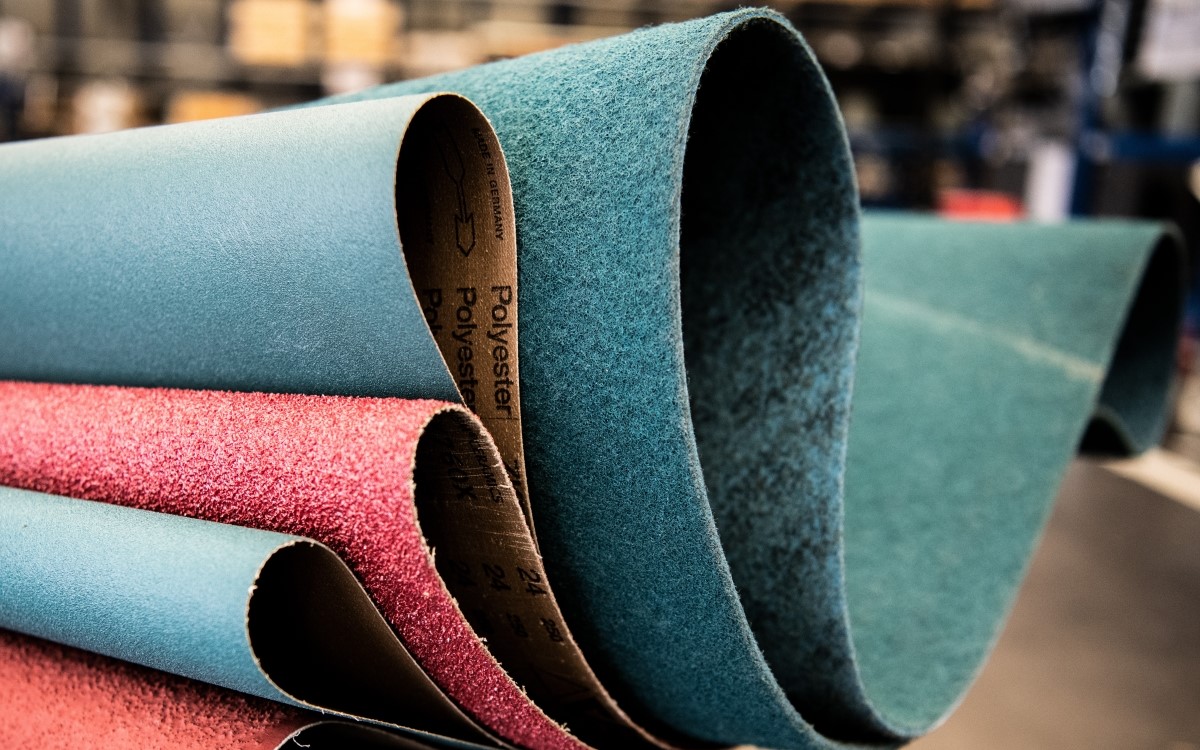
Non-woven abrasives
Non-woven abrasives for surface finishing.