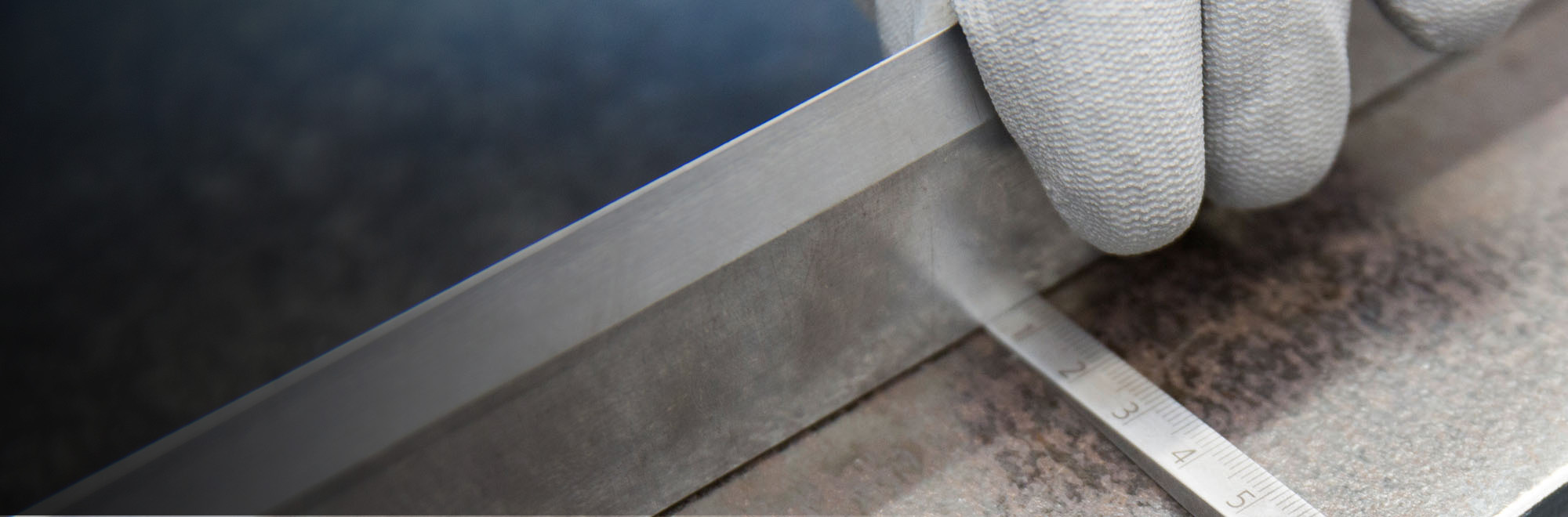
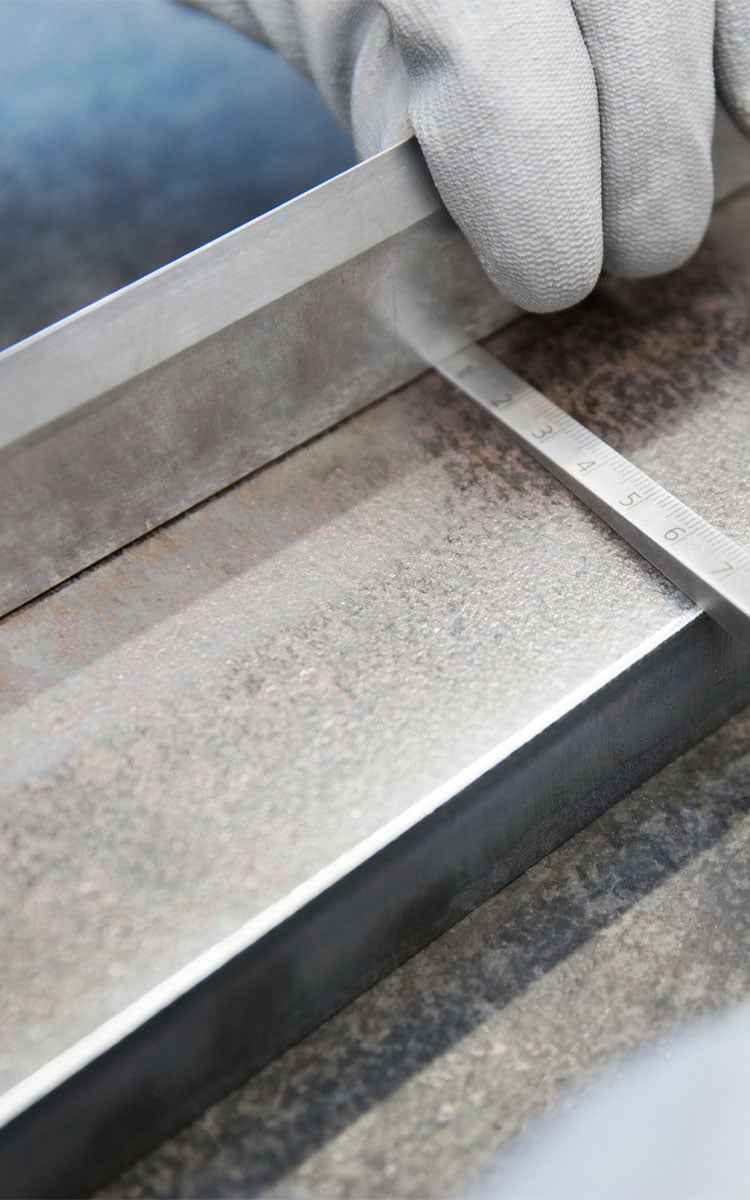
Entfernen Sie Eigenspannungen und Unebenheiten im Blech für bestmögliche Folgeprozesse.
Direkt zu den Maschinen?Richten
Teilerichten sorgt für spannungsarme und ebene Bleche
Wenn aus Blechen perfekte Werkstücke und Baugruppen mit engen Toleranzen entstehen sollen, muss man sich auf das Material verlassen können. Das ist nicht selbstverständlich: Viele Bleche enthalten Eigenspannungen und Unebenheiten. Und die stören bei der Weiterbearbeitung.
Eigenspannungen im Blech können auf unterschiedliche Weise entstehen: Durch das Schneiden mittels thermischer Trennverfahren, wie Lasern oder Autogen- und Plasmaschneiden, wird am Schneidstrahl sehr viel Wärme in das Material eingebracht. Das dadurch entstehende Temperaturgefälle im Werkstoff verursacht Spannungen und Aushärtungen an den Rändern. Die Folge: Die Blechteile weisen nach dem Schneiden Verzug auf. Beim Stanzen wird das Blechteil durch den Stanzvorgang verformt und es werden vorhandene innere Spannungen im Material freigesetzt.
Welche Vorteile hat das maschinelle Richten?
Eigenspannungen und Unebenheiten beseitigen
Das Walzen, mechanische oder thermische Trennverfahren sowie Wärmeeinwirkung können zu Eigenspannungen im Blech führen. Mit einer Richtmaschine beseitigen Sie sie zuverlässig.
Produktionsfehler vermeiden
Eigenspannungen im Blech führen zu Winkligkeitsfehlern beim Abkanten oder Verzug beim Schweißen. Diese Schwierigkeiten können Sie von Anfang an vermeiden.
Enge Toleranzen einhalten
Beim Fügen der Baugruppe zeigt sich manchmal: Die Toleranzen addieren sich zu weit auf. Wer von Anfang an möglichst präzise produziert, kommt gar nicht in diese Verlegenheit. Das gelingt mit gerichteten Blechteilen.
Weniger Ausschuss mit Schweißrobotern
Für eine effiziente Produktion benötigen Schweißroboter Blechteile mit besonders engen Toleranzen. Deshalb ist es wichtig, diese Teile von dem Zuführen zum Roboter zu richten. Ansonsten droht zu viel Ausschuss.
Beim maschinellen Richten mit Richtwalzen (Walzenrichten) durchläuft ein Blech mehrere aufeinander folgende Wechselbiegungen. Vom Einlauf bis zum Auslauf der Richtmaschine sind die Richtwalzen versetzt angeordnet. Dadurch taucht eine Walze immer zwischen den beiden gegenüberliegenden Richtwalzen ein. An den ersten Richtwalzen sind die Wechselbiegungen stark und werden zum Auslauf hin immer schwächer. Der Verlauf der Biegungen ähnelt so einer abklingenden Sinuskurve.
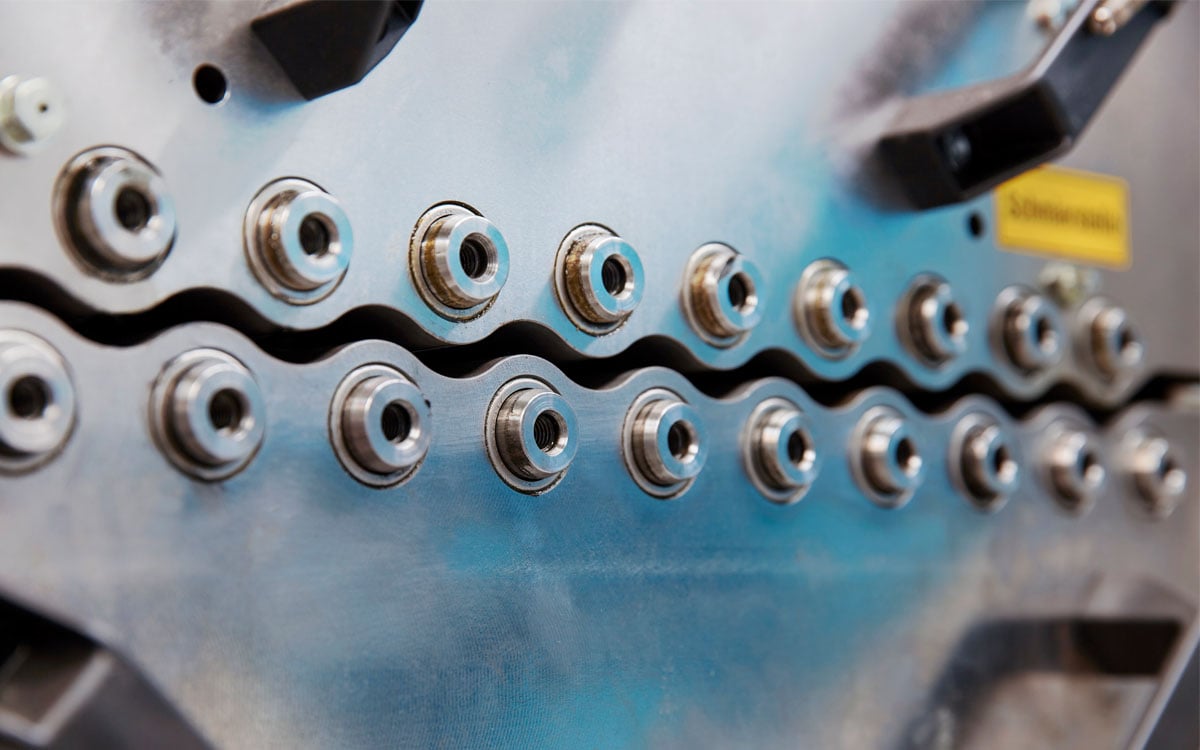
Fakten auf einen Blick
- Durch die elastisch-plastischen Wechselbiegungen und die stetige Verringerung der Umformung entsteht ein ebenes und vor allem spannungsfreies Blechteil.
- Walzenrichtmaschinen richten Ihre Bleche schnell und einfach.
- Grafische Bedienoberflächen ermöglichen eine schnelles und genaues Erreichen der richtigen Einstellungen und machen die Richtmaschinen zugleich einfach in der Benutzung.
Passende Maschinen
Richtmaschinen für Feinbleche, Stanz- und Laserteile
Richtmaschinen für Grobblech und Platten
Unsere servo-hydraulischen Richtmaschinen sind speziell für anspruchsvolle Richtaufgaben konzipiert. Die Richtwalzen sind durch die Hydraulik maximal gestützt und weisen einen geringen Abstand zueinander auf. Dank der integrierten Richtspaltregelung bleibt der Richtspalt während des gesamten Richtvorgangs konstant, selbst bei wechselnden Teilequerschnitten. So können selbst herausfordernde Blechte und Platinen innerhalb kürzester Zeit präzise und spannungsfrei gerichtet werden.
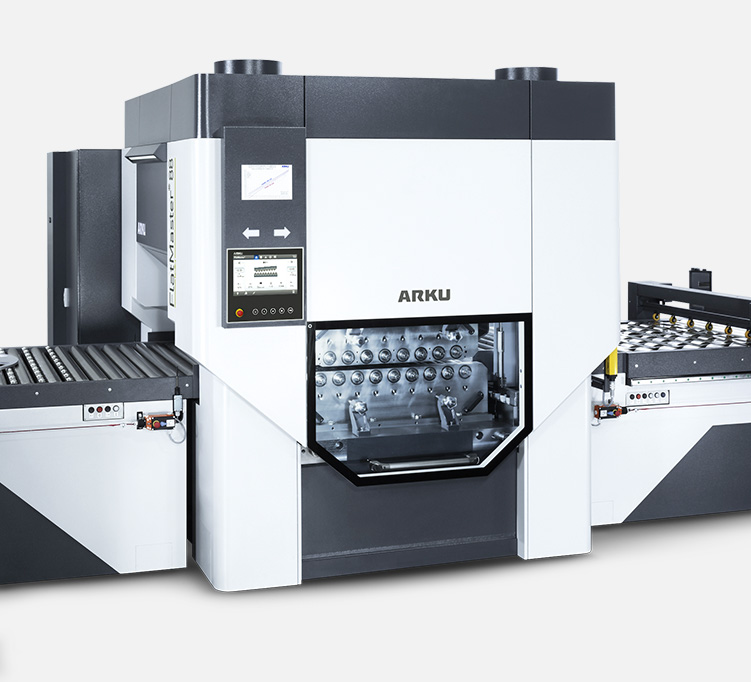
Fakten auf einen Blick
- Schneller und genaue Maschineneinstellung ermöglicht ebene und spannungsfreie Blechteile in Sekunden.
- Hoher Durchsatz vereinfacht das Richten von vielen Bauteilen ohne Flaschenhals in der Produktion.
- Hydraulischer Überlastschutz sichert eine langlebige und unzerstörbare Richtmaschine.
- Leistungsgeregelte Servo-Hydraulik spart Strom und Energie.
- Maximale Kräfte der Hydraulik ermöglichen hervorragende Richtergebnisse selbst bei dicken Brennteilen.
Passende Maschinen
Richtmaschinen für Feinbleche, Stanz- und Laserteile
Richtmaschinen für Grobblech und Platten
Was unterscheidet Richtmaschinen von alternativen Richtverfahren?
Unsere Präzisionsrichtmaschinen stehen dank ihrer Langlebigkeit und Unverwüstbarkeit für eine zuverlässige und sichere Investition. Sie haben verschiedene Vorteile gegenüber alternativen Richtverfahren:
- Ebene und spannungsfreie Blechteile für eine bessere Weiterverarbeitung
- Deutlich schnelleres und effizienteres Richten als mit anderen Richtmethoden
- Intuitive Maschinenbedienung ohne großen Schulungsaufwand
- Nachfolgende Prozessschritte wie Schneiden, Schweißen oder Biegen werden zuverlässiger
- Reduktion von Nacharbeit und Ausschuss
- Wiederholgenaue Ergebnisse, unabhängig vom Mitarbeiter
- Hoher Durchsatz ermöglicht das Richten von vielen Bauteilen ohne Flaschenhals in der Produktion
- Eigenspannungen im Material werden kaum verringert
- Wesentlich zeitaufwendiger als das maschinelle Richten
- Bearbeitungszeit pro Teil von 20 Minuten und mehr ist keine Seltenheit
- Diese Methoden können nur extrem erfahrene Mitarbeiter anwenden
- Schwankungen in den Ergebnissen kommen häufiger vor
Sie benötigen weitere Informationen?
Ob dicke oder dünne Bleche, kleine oder große Teile: Bei den Richtmaschinen von ARKU finden Sie immer die richtige Anlage für Ihre Anforderungen. Wir beraten Sie gerne!