Sheet metal edges should be deburred and rounded; depending on the application, this might already be specified in the drawings. This is because the burrs - sharp metal residues on the edge of the sheet metal can cause interferences and damage. This not only applies to the final product, but also the entire sheet metal process.
7 success factors for efficient processes.
From automated warehouses to intelligently linked machines: find out which factors help to ensure efficient sheet metal processing.
Download: Success factors for efficient sheet metal processing
Automated deburring outperforms manual work by a long shot
The advantages of automated deburring compared to manual deburring are obvious. A modern sheet metal deburring machine works about four times faster than skilled workers with angle grinders. The return on investment can be achieved after only 500 working hours using automated deburring. At this scale, automated deburring is an attractive option, even for smaller companies. In addition, the system operates with repeatable accuracy and process reliability. This guarantees consistent high quality of the final products. In times of a shortage of skilled workers, it is also important that employees can devote themselves to more productive tasks.
Automated deburring also has advantages for employees in other aspects. After all, they must lift sheet metal parts, insert them into machines, stack or assemble them. If burrs are still stuck to the sheet metal edges, employees can get injured.
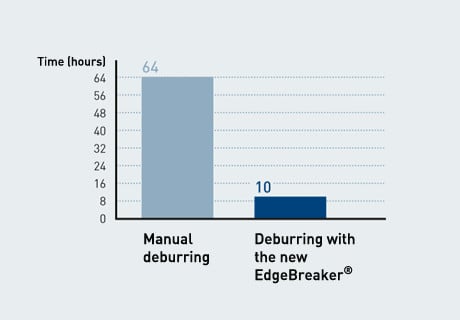
Burrs scratch materials and tools
In addition, not only people, components and their surfaces also get damaged by burrs. This can occur when sheet metal parts are stacked on top of each other, scratching the surrounding parts. The same applies to forming: Straightening rolls and press brake tools wear considerably faster if they repeatedly come into contact with hard burrs. Here as well, automated deburring pays off big time.
Another step in the sheet metal process chain also benefits from deburring: Tools can be clamped and positioned much better if there are no protruding metal residues. This applies above all to milling, which is quite common for thicker plate materials.