More satisfied customers thanks to the ARKU deburring machine.
In 2020, GER4TECH established the new Metal & Mechatronic Center at Redlham in Upper Austria. The company showcases its two divisions, metal and mechatronics, in a production area of 9,600 square meters.
With regard to metal, GER4TECH specializes in sheet metal technology, metalworking including welding technology and surface treatment. Whether individual pieces or large-scale series, simple sheet metal parts, complex assemblies or machine components - the metal technology specialist delivers to customers from various industries. “We always place value on the quality,” GM Hubert Gerstmayr stresses.
In the field of mechatronics, the company implements individual, robot-based automation projects. The system integrator combines industrial robots with user-friendly software and innovative controls. Ultimately, the accell subsidiary complements the offering with simple robot cells for grinding, polishing and deburring. GER4TECH customers for both divisions are small and medium-sized industrial enterprises from Austria, Germany and Switzerland.
Watch the video success story of GER4TECH:
„In the course of establishing our production site in Redlham, we want to advance our production technology in all areas“
Hubert Gerstmayr, CEO at GER4TECH
Although a deburring and edge rounding machine was stationed at the old site, it no longer stood up to the tasks required. „We wanted to achieve the best and most reliable results on both sides of the flat sheet metal in terms of process reliability for our customers“ - Gerstmayr explains further. With the ARKU deburring machine EdgeBreaker® 3000, the optimal solution was quickly found.
Productivity increased with the same number of employees due to double-sided deburring
ARKU has developed the EdgeBreaker® 3000 specifically to quickly and efficiently deburr large quantities of sheet metal parts and round their edges. The system contains two modules with abrasive brushes: The first is used to deburr the workpieces and the second to round the edges. The EdgeBreaker® 3000 is extremely powerful thanks to these deburring and rounding tools.
GER4TECH can now process workpieces on both sides thanks to the EdgeBreaker® 3000. “We are saving half of the time, because the operator no longer needs to remove, turn and insert the workpieces again,” says the Head of Manufacturing. “Compared to the old deburring machine, we are now twice as fast. Despite an increase in volume through the fiber laser and higher customer orders, we were able to work with the same number of employees,“ he continues.
High quality metal sheets guarantee satisfied end customers
Customers’ quality standards have increased. “According to EN 1090, the edges of all components must be rounded before coating,” the managing director explains. There is a reason for this requirement: The coating cover is weak on sharp edges, the liquid film tears off during the coating process. If the paint cover has a weak point on such an edge, the metal below is no longer protected. Atmospheric oxygen and water have free rein, and corrosion will soon follow. Gerstmayr also recalls another reason why customers request rounded edges: “Sharp edges can injure employees during handling or assembly.” No employer and no manager wants to shoulder such a responsibility. “We include deburring and edge rounding of the parts in our offerings right from the start. Naturally that adds to the costs, but more and more customers want it like that,” Sulzberger confirms.
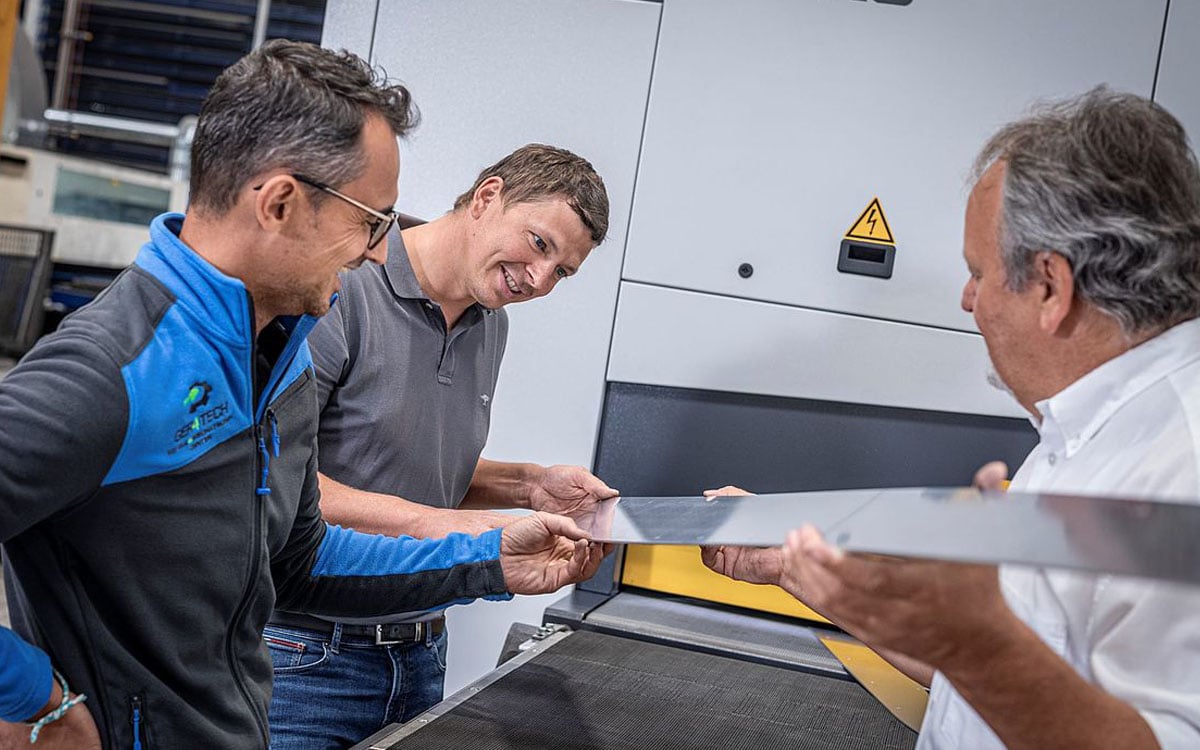
Intuitive operation helps the employees
GER4TECH employees find the new EdgeBreaker® 3000 easy to operate. On the one hand, thanks to double-sided processing, the workload has decreased. On the other hand, they are supported by simple and self-explanatory controls. “Any operator can work with the machine after three to four hours training,” says the manufacturing manager. Compared to the old machine, working is now process-reliable and the result is better.
This is how everyone has benefited from the new EdgeBreaker® 3000 from Baden-Baden: The employees are able to increase quality with ease; customers receive perfectly deburred and rounded sheet metal parts as desired. And within the tough competitive environment of contract manufacturers, GER4TECH has added another advantage to cement their commitment to quality.